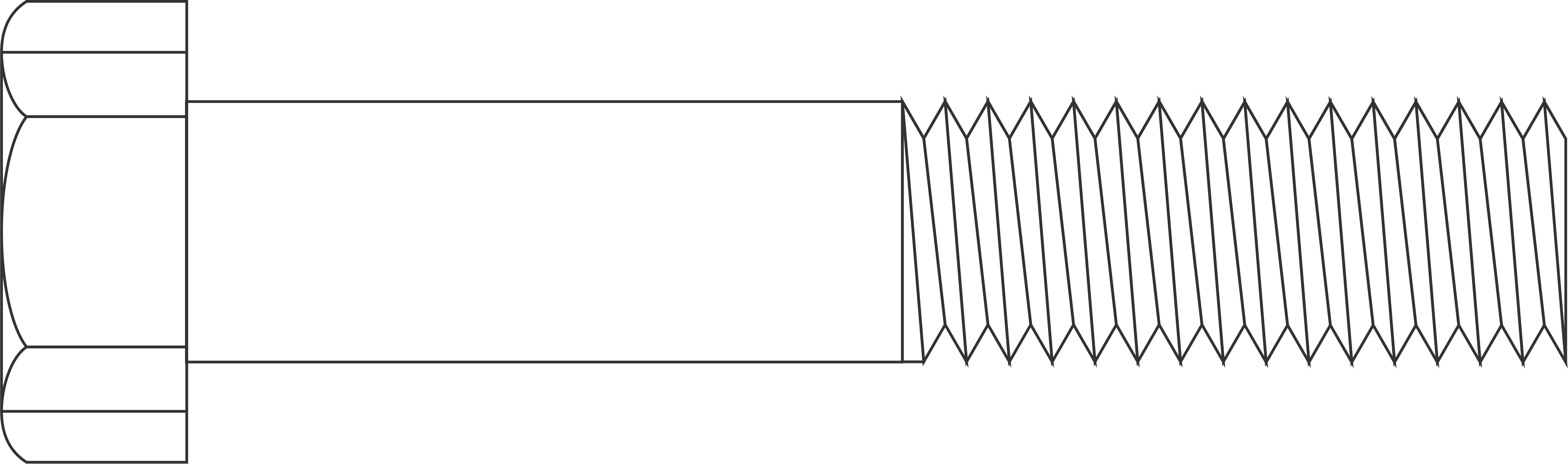
SOMETIMES IT’S NOT ENOUGH TO JUST TURN SOME SCREWS.
Sometimes it´s not enough to just turn some screws.
Would you like to purchase screws, fixings and fasteners efficiently and cost-effectively? No problem, we offer you a wide range of customised logistics solutions and customised services for all aspects of C-parts management. This allows us to increase your efficiency and reduce the costs of C-parts procurement. However, before we decide to implement our C-parts management together with you, a number of conceptual and organisational steps need to be considered. These measures are necessary to increase the efficiency of the system, to select the appropriate information channels and to offer you the best solution for your supply security.
Classically analogue, optically via barcode scanning or digitally via RFID
We offer you state-of-the-art technologies for communicating your demand requirements to ensure that workflows, processes and idle capacities are used efficiently. All transmission options for your data are coordinated with you to develop a tailor-made solution for your demand communication. This ensures permanent availability and demand-driven delivery, as well as optimal use of storage space.
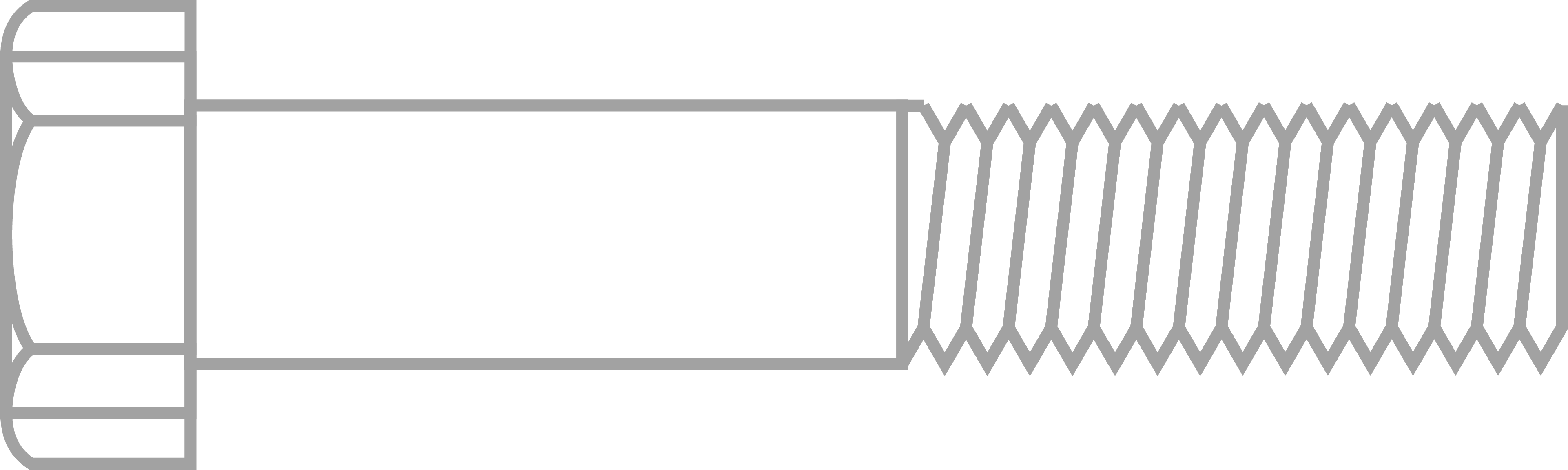
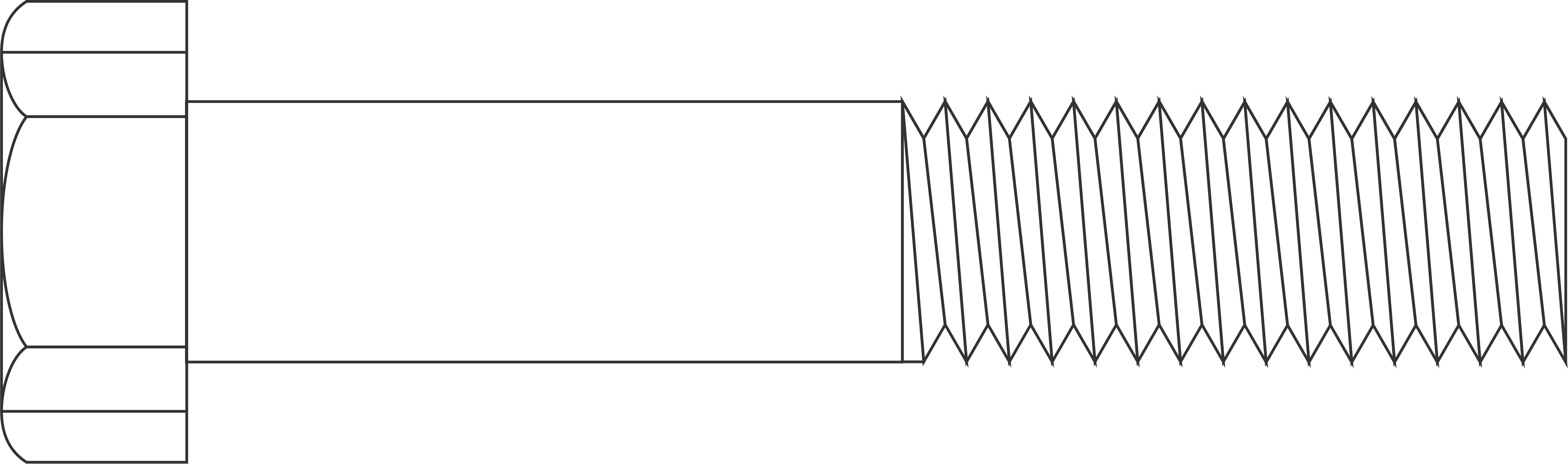
eWA – 5 tailored solutions
WATERMANN offers five solutions in the field of C-parts management, which we can adapt, of course, to your individual requirements.
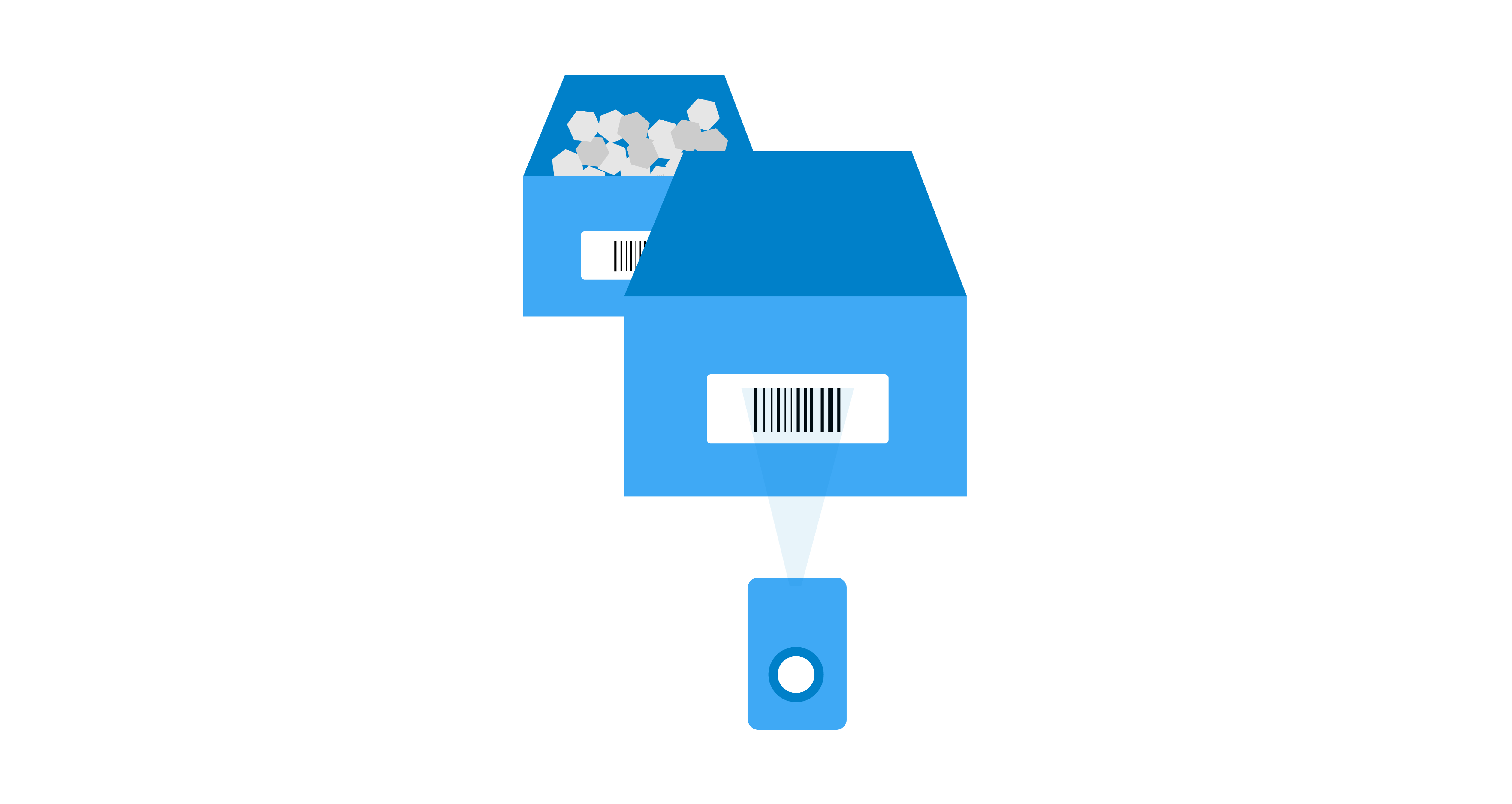
eWA 1 – check
Two-bin KANBAN system:
The bins permanently remain at the CUSTOMER'S
- As soon as a bin is empty, the CUSTOMER triggers the reordering of items by scanning and data transfer to WATERMANN (via online link, email, fax, etc.)
- Delivery to incoming goods department; replenishment of the bins and shelf storage by the CUSTOMER
eWA 2 – check & fill
Two-bin KANBAN system:
The bins permanently remain at the CUSTOMER'S
similar to eWA 1, plus:
Replenishment of the KANBAN bins at the CUSTOMER’S site by WATERMANN or the logistics partner
eWA 3 – check, fill & get
Two-bin KANBAN system:
Replenishment of bins at WATERMANN'S
- After withdrawal, the empty bins are made available for collection at the empty bin collecting point. This automatically triggers reordering.
- Delivery of the replenished KANBAN bins to the incoming goods department and collection of the empty bins for replenishment at the same time.
eWA 4 – complete
Two-bin KANBAN system:
All steps of the KANBAN cycle are performed by WATERMANN or the logistics partner
similar to eWA 3, plus:
Putting the replenished KANBAN bins into the CUSTOMER’S shelf system by WATERMANN staff or the logistics partner
eWA 5 – simple
One-bin KANBAN system:
Containers permanently remain at the CUSTOMER'S
- Reordering by scanning the empty KANBAN bins at the CUSTOMER’S
- The replenishment of the bins is performed by request either by the CUSTOMER or by WATERMANN or the logistics partner
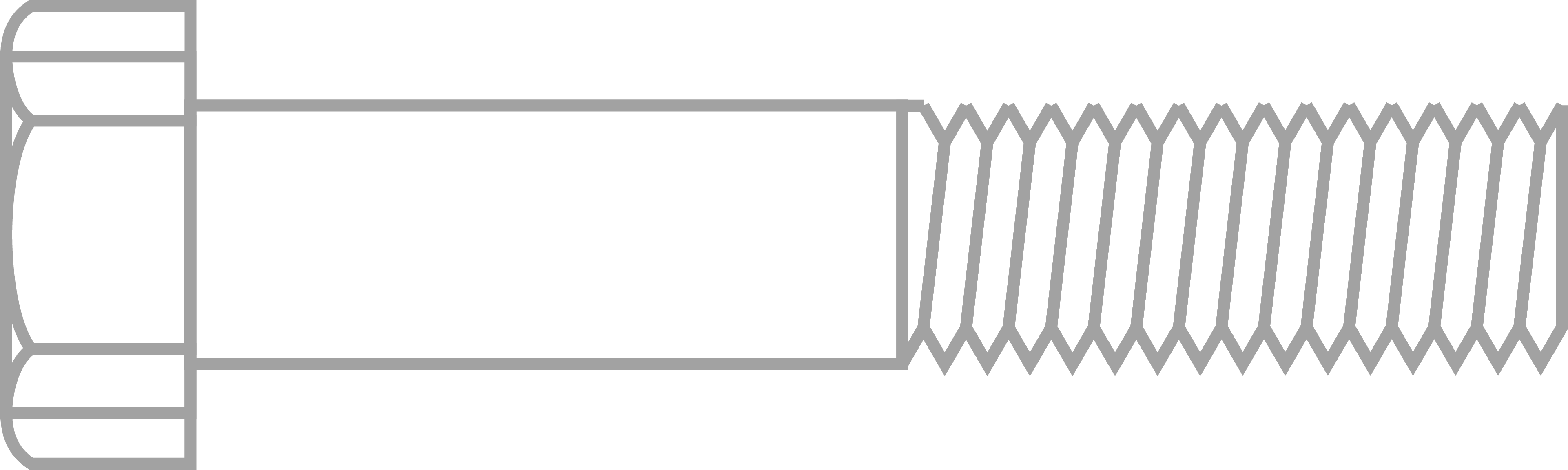
KANBAN – Systematically Saving Costs
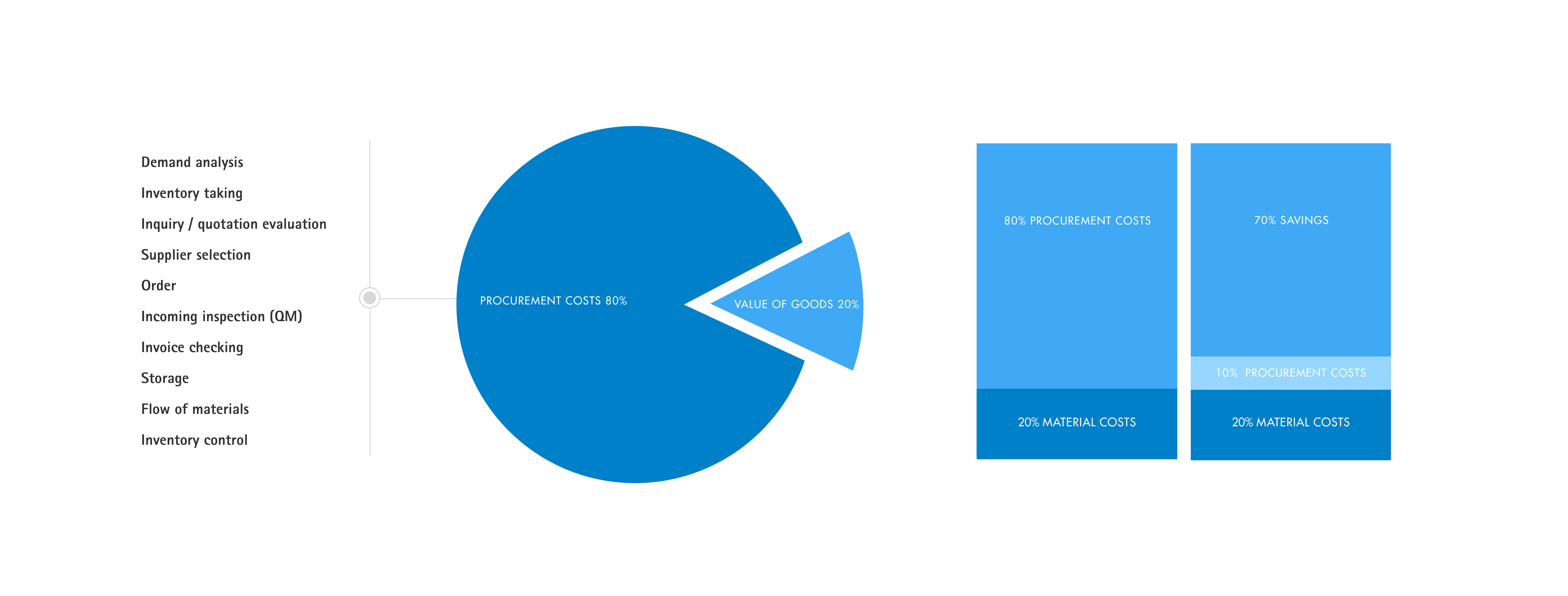
Feasible savings are only obtainable by optimising the order and delivery processing while simultaneously reducing logistics-related expenses.
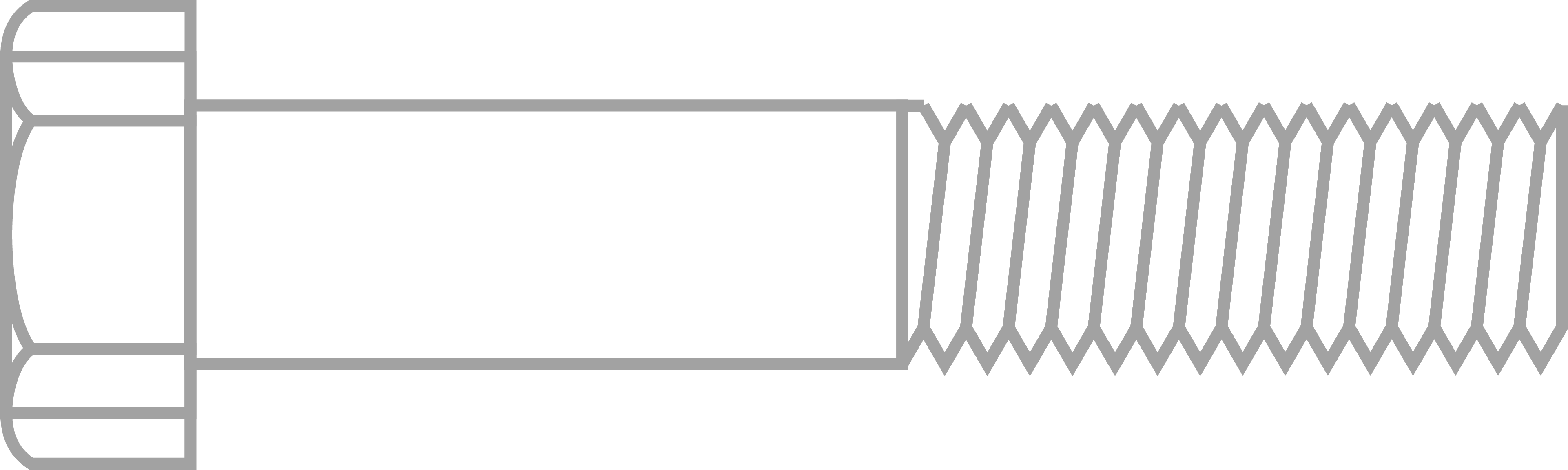
KANBAN Procedure in Detail
1. Preparatory phase
Watermann
· Elaboration of a KANBAN concept
· Provision of technical equipment
· Determination of shelf and bin labelling
·Material flow analysis for optimum system layout
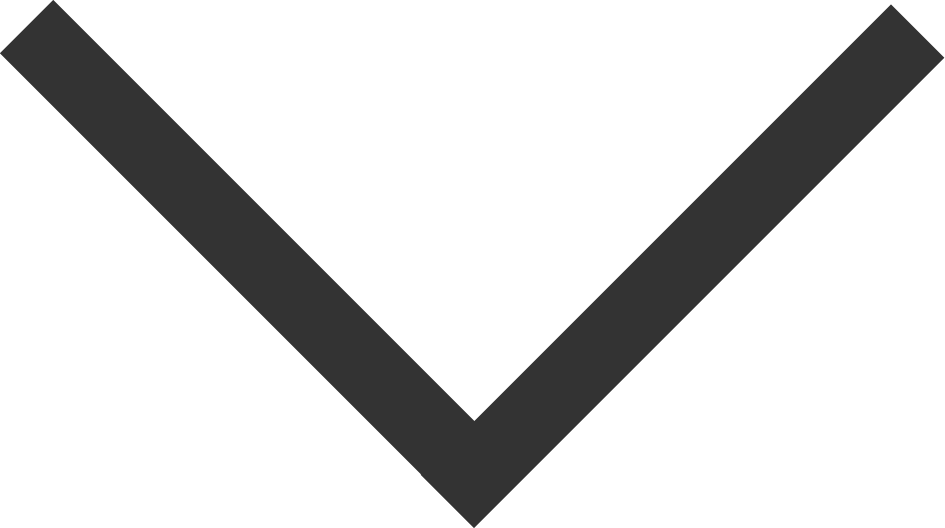
CUSTOMER:
· Determination of the product range and corresponding rates of consumption
· Number and specification of supply areas
2. Implementation phase
Watermann
· Filling of shelves with bins and material
· Labeling of shelves and bins
· Staff instruction in KANBAN handling
· Installation of barcode scanner including instructions
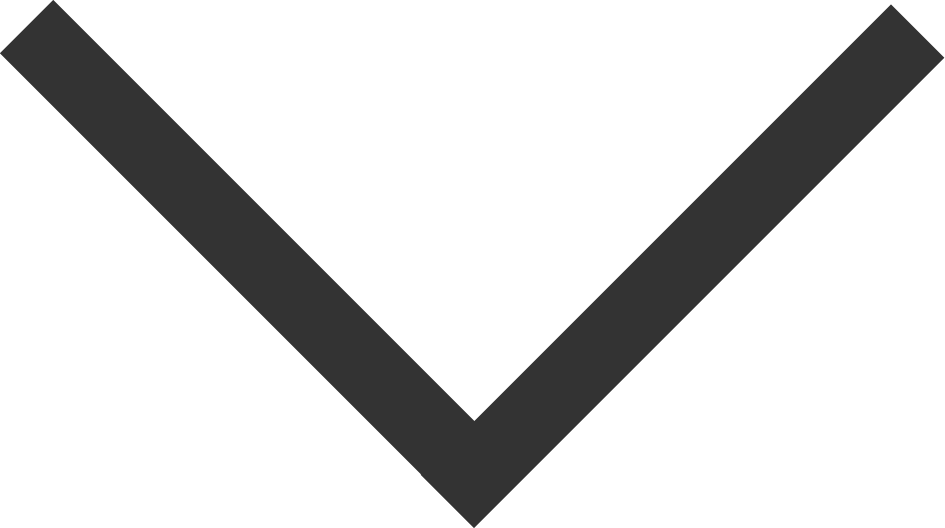
CUSTOMER:
· Provision on storage space
3. System maintenance
Watermann
· Consumption-oriented replenishment of the KANBAN system
· Flexible item optimization within the range of products
· Expansion of shelf modules in case of new items
· Ensuring process control for continuous optimisation, including the determination of further feasible savings
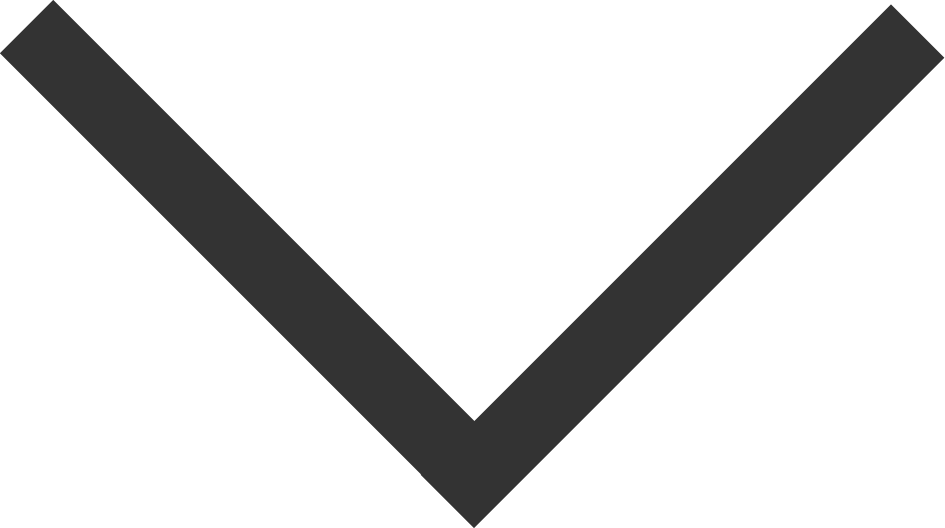
CUSTOMER:
· Information on extending the range of products
· Information on production changes affecting the product range and the quantities in stock
Your advantages at a glance
· Process cost reduction
· Reduced capital tie-up due to storage capacity reduction
· Reduction of the number of suppliers
· System support including product range maintenance by WATERMANN
· Maximum reliability of supply
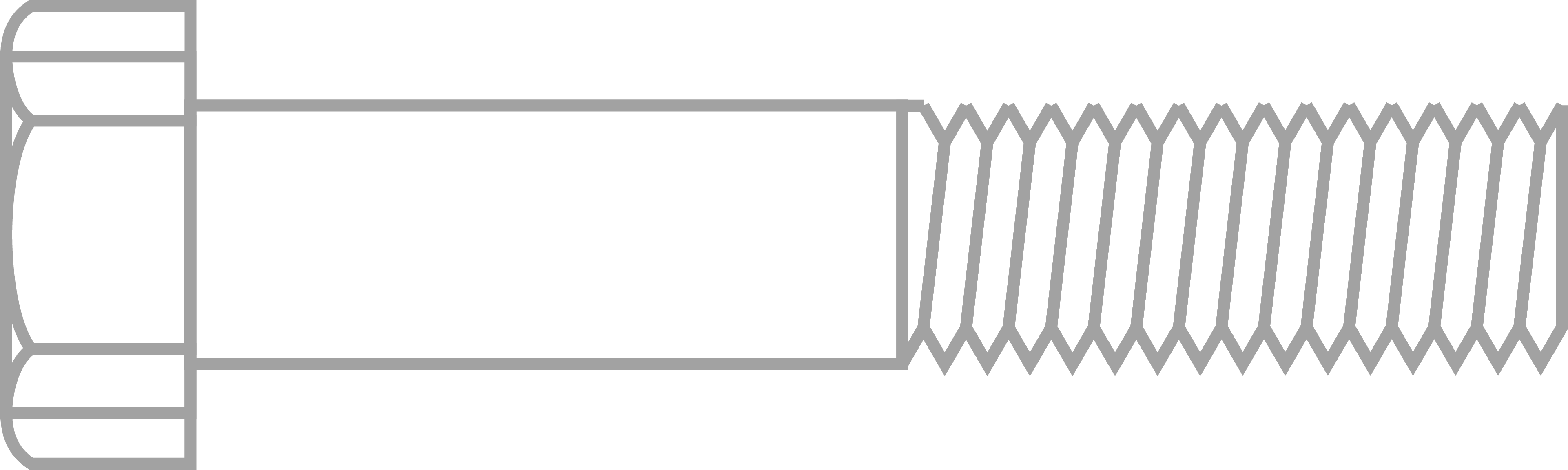
e-Business and Process Cost Optimisation
The e-business and process cost optimisation topics are also part of KANBAN.
In this respect, WATERMANN offers various possibilities:
- Electronic data interchange (EDI) of business documents using various interchange formats (EDIFACT, CSV, EXCEL, XML, OpenTRANS®, etc.).
- Electronic catalogues – also tailor-made – in diverse formats (BMEcat, for example) with common classifications (eCl@ss®)
for your e-procurement system.
- WATERMANN online shop – more than 40,000 items are always retrievable. Standard parts as well as other parts can be ordered by different features and search criteria.
- Optimisation of procedures by using bar codes on delivery notes, invoices and other business documents.